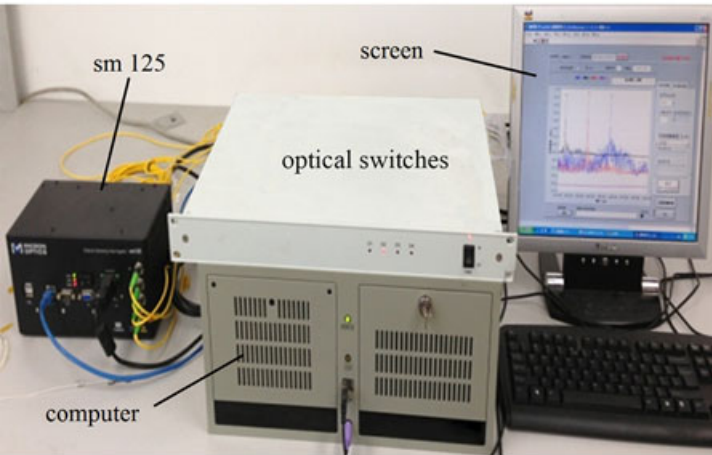
中文摘要:在地球的正常环境中,有几种方法可以获得卫星翼架的挠度曲线,如激光法和电阻应变仪法。然而,它们都不适用于外太空环境。因此,开发一种可靠的传感解决方案,用于高电子噪声、真空和极低温度环境,可能是一项非常具有挑战性的任务。本文提出了一种新的光纤布拉格光栅(FBG)传感器方法,以满足这种恶劣环境的需求。首先,将数百个FBG传感器粘贴在卫星翼架的表面上,以检测应变数据。其次,使用三次样条插值函数、二次积分函数和量子多项式函数进行数据处理,以获得卫星翼架的形状。最后,将卫星翼架放置在散热器中进行形状监测实验。此外,在正常环境中的验证实验表明了FBG传感器方法的可靠性。由于FBG传感器和配套设备在市场上都有售,因此这种方法是外太空形状监测的可行解决方案。
英文摘要:In a normal environment on Earth, there are several methods for obtaining the deflection curve of a satellite wing frame, such as the laser method and the electronic resistance strain gauge method. However, none of them are suitable for the outer space environment. Therefore, developing a reliable sensing solution for a high electronic noise, vacuum, and extremely low-temperature environment may be a very challenging task. In this paper, a new fiber Bragg grating (FBG) sensors method is proposed to meet this harsh environment need. First, hundreds of FBG sensors are pasted onto the surface of a satellite wing frame to detect the strain data. Second, the cubic spline interpolation function, quadratic integral function, and quantic polynomial function are used for the data processing to obtain the shape of the satellite wing frame. Finally, a satellite wing frame is placed in a heat sink to conduct a shape monitoring experiment. Furthermore, a verification experiment in a normal environment shows the reliability of the FBG sensors method. Because the FBG sensors and the supporting equipment are available in the market, this method is a feasible solution for shape monitoring in outer space.